ラベル製造装置における非粘着・離型コーティング適用事例|プラズマコーティング
ラベル製造装置のニップロールに対する粘着物(ホットメルト)付着防止の対策として、弊社のプラズマペーパーをご採用いただきました
Before
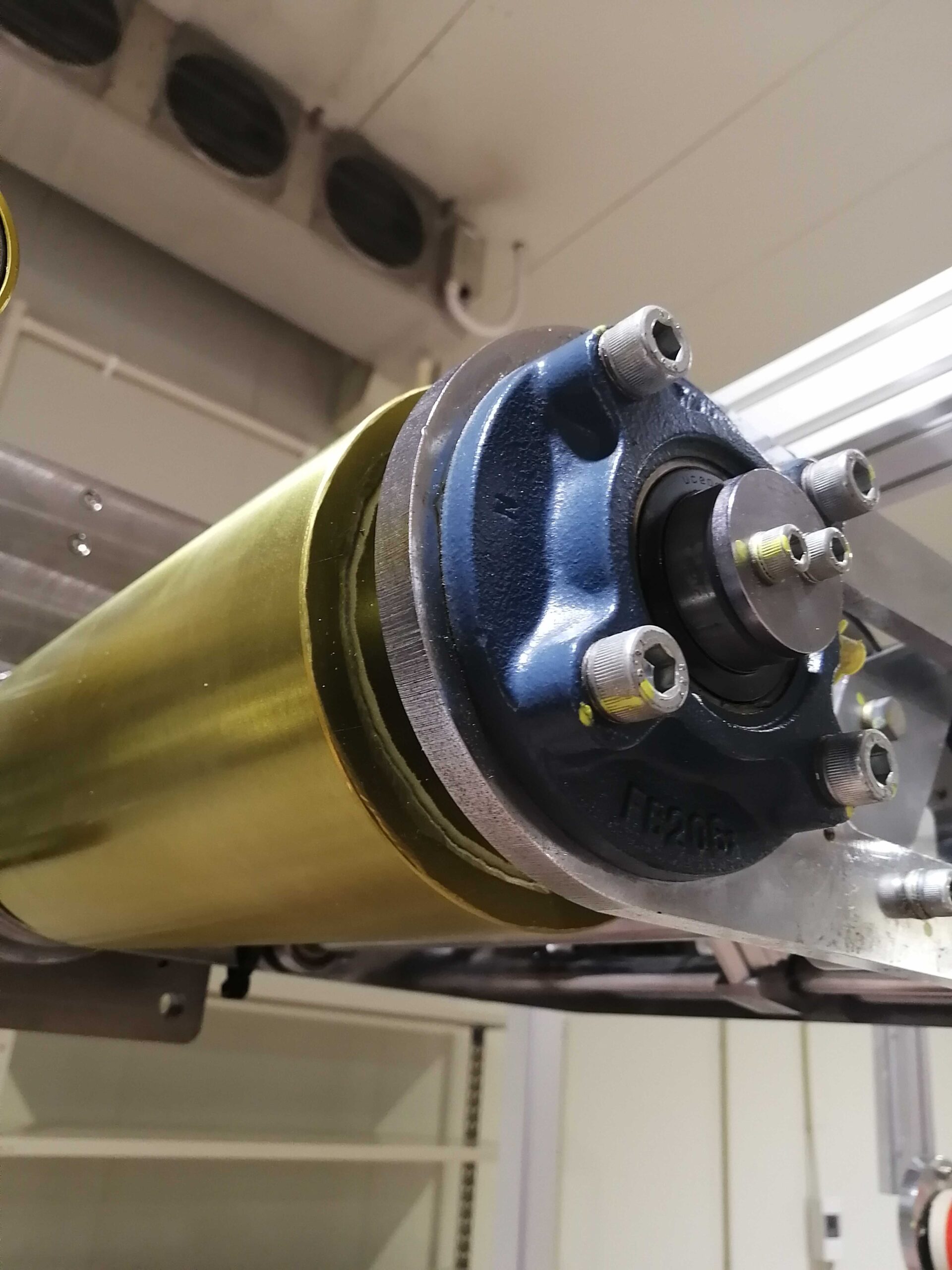
After
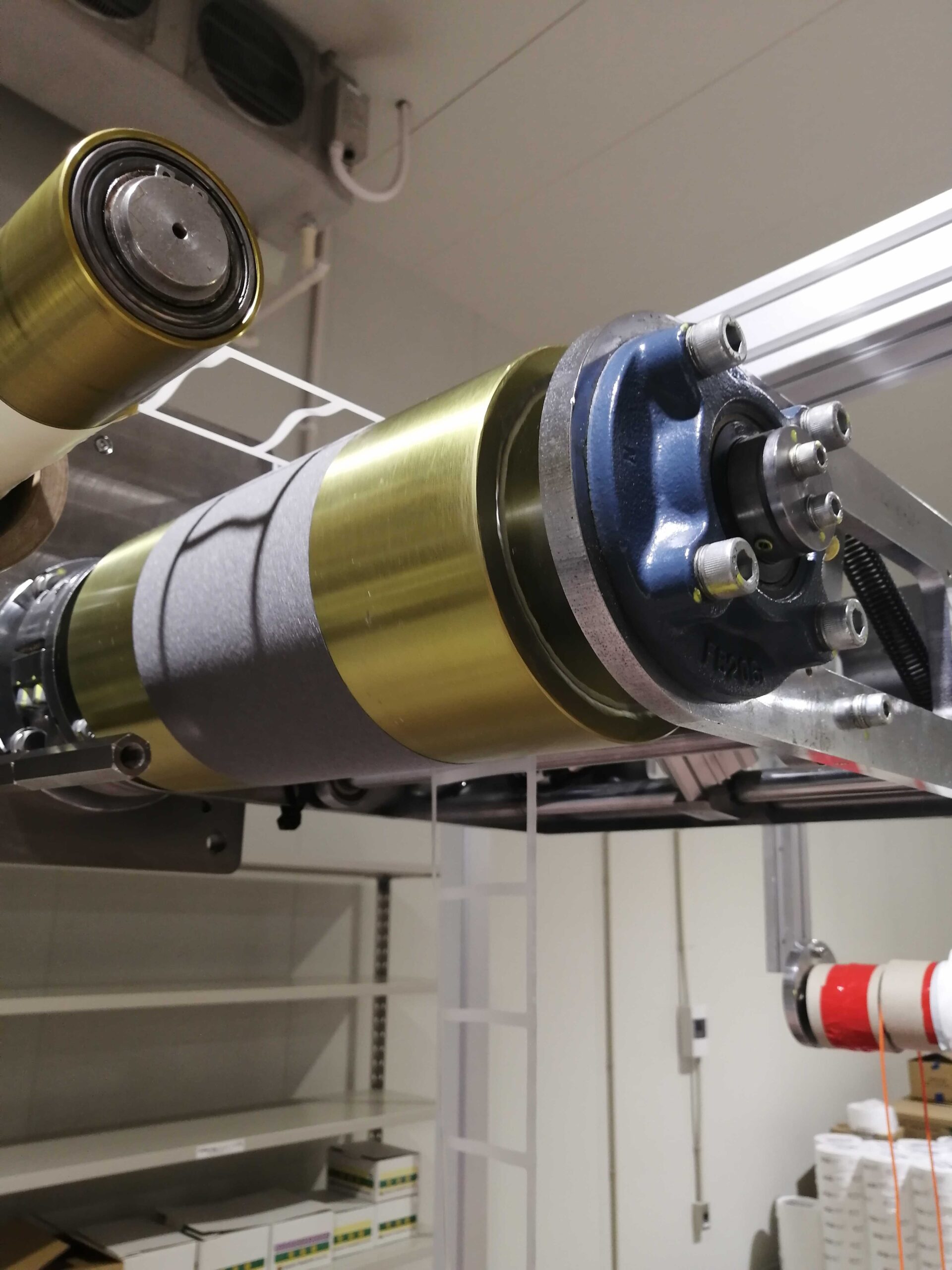
施工後のロールの様子
お客様の課題
ラベル製造工程では、粘着物(ホットメルト)の付着が大きな課題となっている。
特にカット後のトリム部分が搬送ニップロールに粘着物が付着することで生産効率の低下やメンテナンス作業の増加が発生していた。
- 粘着物の付着によりトリムの搬送がスムーズに行われない。
- 既存の対策(ガラステープやフッ素テープなど)は十分な非粘着性が得られない上に、耐久性も低くすぐに効果が消失してしまう。
- 頻繁な清掃作業が必要となり、歩留まり率が低下。
また、そのような課題は設計時点では中々予測が難しく、実際に現場で納入して初めて粘着物付着する箇所が判明する為、すぐに離型・非粘着コーティングを施した設備・ロールの新規作成はコストや手間が大きく難しい。
また、製造ラインの現場エンジニアが使える簡易的なソリューション(ガラステープや非粘着テープ)ではその性能が高くなく、解決に至らないことがしばしば。
カンメタエンジニアリングの提案
お客様自身でカットでき、その非粘着・離型効果が非常に高いプラズマペーパーをロールに巻き付ける方法を提案いたしました。
既存装置・部品に対する短期間での非粘着・離型性実装を実現しました。
結果
(1)性能向上
- その場でホットメルトの付着を防止。
- 粘着物の搬送がスムーズになり、生産効率が大幅に改善。
- 清掃作業の時間が短縮され、必要人数も削減。
- ロールの交換頻度が低減し、コスト削減にも寄与。
- プラズマペーパーにより製造現場で迅速に初期テストを実施でき、効果検証が可能。
- 迅速に現場での仕様選定が可能となり、将来設計仕様としてロールに直接施工を行うプラズマコーティング技術の本格採用検討を進める。